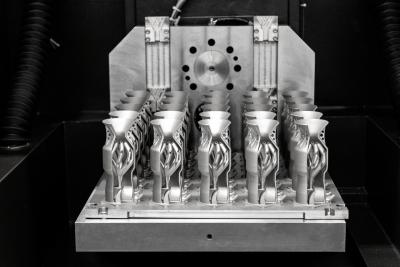
In 2021, United Performance Metals opened its doors to its brand-new additive manufacturing facility in Cincinnati, Ohio. With additive manufacturing on the rise, United Performance Metals wanted to add to their array of services and provide high-quality solutions to its additive manufacturing customers.
Additive manufacturing, often referred to as AM or 3D printing, is a process that creates three-dimensional objects layer by layer from a digital model. This process uses computerized machines to plan and build pieces with a variety of materials, from metal to plastic, and even food!
Additive manufacturing has the capability to create complex, precise objects in an efficient manner, which often uses less material, resulting in saved time and cost. AM can be used in a variety of industries, including aerospace, space, defense, and medical. Some of the applications in these industries include customized prosthetics, dental devices, engine parts, and more!
There are three main types of additive manufacturing: powder bed fusion, direct energy deposition, and material extrusion. While these processes are similar, the methods utilize different materials and resources and can yield different outcomes.
- United Performance Metals Additive Solutions is involved in the powder bed fusion process, which joins powdered material using fiber optic lasers or electron beams. These processes melt and fuse the material together, going layer by layer until the model is complete. The powder bed fusion process requires a roller or blade recoaters that spreads the powder material evenly as each layer is created. PBF recoater blades and powders are just a few of the many ways that UPM Additive Solutions assist the additive manufacturing industry. The Powder Bed Fusion technique only melts the powder it needs to create each layer, resulting in reduced waste. Any unused powder can be recycled and reused in other builds. PBF can work with ceramics, glass, plastics, metals, and alloys, making it a versatile printing option.
- The DED process starts with an axis arm that deposits material from a nozzle. The deposited material is either a wire or powder form that is then melted using a laser, electron beam, or plasma arc. This process goes layer by layer until the model is complete. DED has the ability to control the grain structure, allowing it to be used for the repair of high-quality parts. Metals, alloys, ceramics, and some polymers can be used in the directed energy deposition process. In most cases this process will build a near net shape that will be machined to finished dimensions. This technology is great for prototype castings and low volume production parts.
- Material extrusion is the third form of additive manufacturing. This process uses a spool of material that is fed through a heated nozzle. Once heated, the material is melted and deposited out of the nozzle and onto the build platform. Like the rest of the additive processes, material extrusion goes layer by layer until the model is complete. Material extrusion typically uses thermoplastic polymer that is fed through and heated. This process is what many people think of when they hear 3D printing since it is the process that is used for most home 3D printers, and it is traditionally the most inexpensive.
There are several other forms of additive manufacturing, including VAT photopolymerization, material jetting, binder jetting, and sheet lamination. In total, these seven additive manufacturing methods can create a wide range of models using advanced technology.
United Performance Metals Additive Solutions offers a variety of additive manufacturing services that are crucial to the AM process. These products and services create a holistic experience for additive manufacturing customers, allowing for saved time and cost.
Build Plates: United Performance Metals has an additive build platform program that provides precise and reliable prints. Build plates are an integral part of the AM process, serving as the foundation of the 3D printing. UPM’s build plates come in several grades of nickel, titanium, stainless steel, copper, steel, aluminum, and more, with customizable sizing, shape, and finishes to meet industry needs. The plates have treated surfaces that optimize adhesion and prevent warping, ensuring a stable and durable platform for any build needs.
As part of the build platform program, United Performance Metals has a resurfacing program to help extend the lifespan of the build plates and optimize their performance. This program ensures proper leveling, adhesion, and print quality while prolonging and preserving the plates’ integrity. This program is a comprehensive inventory supply chain management solution that is tailored for each customer to help manage build plates, refurbishment, scrap handling, and logistical operations. With a focus on sustainability and cost-effectiveness, the program offers a seamless blend of innovation and expertise to enhance additive manufacturing operations.
Part Cut Off Solutions: Expert EDM specialists at UPM Additive Solutions use state-of-the-art GF Cut AM 500 Wire EDM equipment with interchangeable tooling. The technique known as wire EDM is used to separate metal components that have been additively manufactured from build plates while maintaining geometric accuracy and guaranteeing assembly readiness. This advanced technology makes it possible to generate complex cuts, producing outcomes that surpass even the most demanding standards of precision engineering. Part cut-off is designed to cut parts on any powder bed fuser, reducing total build time and ensuring supports are removed and parts are fully protected.
Wire Feedstock: United Performance Metals Additive Solutions offers high-quality wire feedstock that is engineered to meet the demands of modern industries, ensuring optimal performance, consistency, and reliability. The wire feedstock is manufactured using the finest raw materials, guaranteeing high purity and consistency. UPM’s feedstock comes in a variety of grades of nickel, titanium, and stainless in a range of coil sizes to meet the specific requirements of our clients’ projects.
Powder: A comprehensive range of high-quality metal powders designed specifically for use in Powder Bed Fusion (PBF) machines is available at UPM Additive Solutions. This powder is exceptionally pure and offers enhanced performance and reliable quality. UPM carries Nickel 718, Nickel 625, and Stainless 316 powder materials.
Re-Coater Blades and Heat Shields: Engineered from high-quality materials, UPM’s additive manufacturing re-coater blades are meticulously crafted to ensure smooth and uniform powder deposition for each build. Additionally, UPM’s heat shields provide effective thermal insulation, minimizing heat transfer and establishing consistent build chamber temperatures for optimal printing conditions.
Posted December 02, 2024
Return to Blog