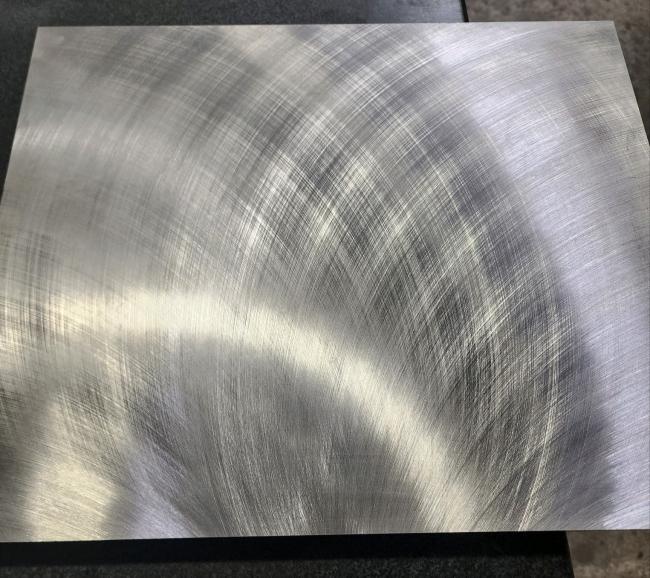
Grinding includes several different processes to achieve precise dimensions and specs by removing small amounts of material from a metal part surface. When it comes to grinding stainless steel and aluminum, specialized equipment and tooling play a crucial role in achieving precise customer specifications. These machines are capable of providing a smooth, polished finish while maintaining dimensional accuracy. Accuracy is key in this process and tools like calipers, micrometers, and surface roughness testers are used to ensure the desired specifications are met. Not only does grinding lead to time and cost savings, but it also contributes to sustainability efforts, minimizing material waste and energy consumption.
At United Performance Metals, we use advanced techniques to achieve the tolerances and the surface finishes that your material requires. We have the specialized tooling and measuring equipment to help achieve your custom specifications and streamline your manufacturing process to limit steps and improve efficiency to save time and cost.
Standard Finish Tolerances
In house we can provide precision ground versions of various grades of our stainless and aluminum plate alloys. We have the capability to grind external customer provided materials as well. We have a broad range of stock removal capability ranging from minimal clean up to heavy stock removal per customer specifications. Standard tolerances include thickness +/- .005”, flat and parallel w/I .005” and surface finish at 63 RMS. We can achieve tighter thickness tolerances, flat, parallels and surface finishes upon request, subject to material and part sizes.
Blanchard Grinding
Blanchard grinding is identified as one of the most efficient methods of achieving finishing flat surfaces on virtually any material. This flat finish is produced by using a vertical grinding spindle with a cylindrical grinding wheel and flat magnetic chuck to hold ferrous material to be finished. As the magnetic chuck rotates, this action helps carry the work under the sides to remove the material. The rotary motion of the grinder allows work to be loaded in a full circle so there are no end pieces.
Double Disc Grinding
Double or Dual Disc grinding is a process that uses abrasive wheels on opposite sides of each other, grinding and removing equal amounts from both sides of material. This process will also produce the highest level of flatness and parallelism on opposing surfaces. Generally, this process is used for high productivity jobs.